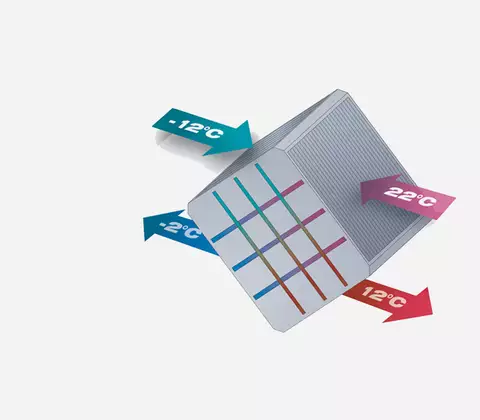
Heat recovery
Almost no heat is lost
Individually planned energy recovery systems configured to suit the requirements can utilise previously generated heat, moisture and cooling in a technically effective and economical manner. This reduces the consumption of primary energy sources in the long term and has a positive effect on the payback period of the system. The capacity of the system being installed can be significantly downsized, thereby also reducing investment and operating costs. The use of energy recovery systems is a mandatory requirement of many national and international standards and regulations and must be documented.
In addition, WOLF heat recovery systems are designed to minimise the proportion of recirculated air. This makes it near impossible for particles carrying viruses to pass from the extract air into the supply air. A huge range of high-efficiency plate and thermal wheel heat exchangers are available for WOLF AHU appliances. We developed a high-performance run-around coil system for use in our modular units. Recirculated air is completely eliminated due to the full separation of the intake and extract air flows.
The perfect solution for heat-recovery AHU appliances with low to medium air flow rates.
Plate heat exchangers function as recuperative heat recovery systems. They are primarily used in air handling units with low to medium air flow rates. Plate heat exchangers are ideal for circumstances that require robust, low maintenance and highly efficient equipment that can also prevent any moisture from being transferred to the supply air.
Countercurrent heat exchangers
Plate heat exchanger
Using previously generated heating or cooling energy in a manner that is both technically and economically efficient is both an ecological and sustainable practice. It is also extremely worthwhile for those operating and investing in air handling systems from a business point of view.
- Efficiency rate of up to 90%
- Failsafe and low maintenance as no moving parts present.
- No transfer of moisture or odour
- Continuous adjustment of output by using the bypass function
- Integrated bypass especially useful in summer
- Suitable for adiabatic extract air cooling
- Ice guard function
- Special aluminium plates for high corrosion resistance
- Completely silicone-free
- Extremely hygienic
Highly efficient crosscurrent heat exchanger (KGXD)
Plate heat exchanger
Using previously generated heating or cooling energy in a manner that is both technically and economically efficient is both an ecological and sustainable practice. It is also extremely worthwhile for those operating and investing in air handling systems from a business point of view. WOLF high-efficiency plate heat exchangers with heat recovery factors of up to 80% work extremely reliably in applications with low to medium air flow rates and are inexpensive to buy.
- Efficiency rate of up to 80%
- Failsafe and low maintenance as no moving parts present
- No transfer of moisture or odour
- Continuous adjustment of output by using the bypass function
- Integrated bypass especially useful in summer
- Suitable for adiabatic extract air cooling
- Optional integrated recirculation
- Ice guard function
- Low pressure losses
- Temperature-resistant up to 90°C
- Special aluminium plates for high corrosion resistance
- Completely silicone-free
- Extremely hygienic
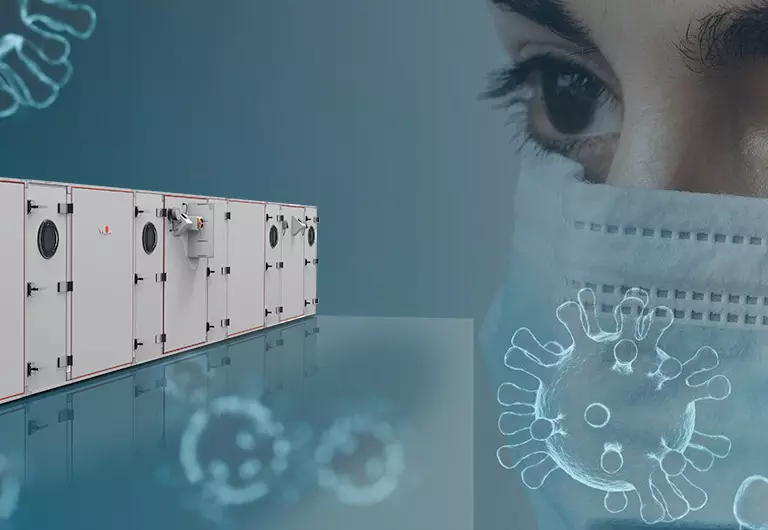
Highest hygiene standards
Air is treated like food in our air handling units (AHUs). With well thought-out technical solutions and an optimal unit design, our claim goes beyond the fulfillment of hygienic standards.
Coupled with proper operation and regular maintenance according to VDI 6022, WOLF ensures hygienic air exchange in buildings.
Flexible heat recovery with a compact footprint
Thermal wheel heat exchangers are just one type of regenerative heat recovery system. They can be used in facilities across the entire range of air flow rates. With the benefit of their compact design and ability to transfer high heat recovery outputs, they are especially effective in higher air flow rate ranges. The rotors owe their universality to their special design, with the base material, installed depth, wave height and diameter all being freely selectable. Whether energy is recovered with or without moisture transfer depends on the base material chosen and its coating.
Condensation rotor
Thermal wheel heat exchanger
The condensation rotor consists of a rotor accumulator that transfers the heat. The rotor is driven by a small motor via a belt. One half of the rotor is located in the extract air, and the other in the supply air. The accumulator is located in the extract air flow and is warmed by this air in winter mode. The rotor turns slowly around its centre axis. The thermal energy is returned to the fresh supply air and warms it.
- Efficiency rate of up to 85%
- High transfer rate with low space requirements
- Many applications due to high level of flexibility
- Variable output control by changing rotation speed
- Summer bypass by stopping rotor
- Low pressure loss
- Self-cleaning mode
- Continuous operation as no defrost bypass necessary
Enthalpy rotor
Thermal wheel heat exchanger
The rotor accumulator has a hygroscopic surface and can transfer both energy and moisture. The rotor is driven by a small motor via a belt. One half of the rotor is located in the extract air, and the other in the supply air. The accumulator is located in the extract air flow, and is warmed by this air in winter mode. At the same time, the rotor's hygroscopic surface absorbs the water vapour created. With the rotor turning slowly, the thermal energy and water vapour are returned to the cold, dry and fresh supply air.
- Efficiency rate of up to 85%
- High transfer rate with low space requirements
- Optional moisture transfer
- Many applications thanks to high level of flexibility
- Variable output control by changing rotation speed
- Summer bypass by stopping rotor
- Low pressure loss
- Self-cleaning mode
- Continuous operation as no defrost bypass necessary
Sorption rotor
Thermal wheel heat exchanger
The rotor accumulator of the sorption rotor has a hygroscopic coating and regulates the transfer of both temperature and moisture all year round. The rotor is driven by a small motor via a belt. One half of the rotor is located in the extract air, and the other in the supply air. The accumulator is located in the extract air flow, and is warmed by this air in winter mode. At the same time, the rotor's hygroscopic surface absorbs the water vapour created. With the rotor turning slowly, the thermal energy and water vapour are returned to the cold, dry and fresh supply air. The process can also be reversed which makes the sorption rotor ideal for summer mode as well. The ability to operate in reverse can save a huge amount on the cost of cooling energy.
- Efficiency rate of up to 85%
- High transfer rate with low space requirements
- Optional moisture transfer/dehimidification
- Many applications thanks to high level of flexibility
- Variable output control by changing rotation speed
- Summer bypass by stopping rotor
- Cooling in summer mode
- Low pressure loss
- Self-cleaning mode
- Continuous operation as no defrost bypass necessary
Highly efficient heat recovery throughout the entire system
Highly efficient heat recovery is possible, even in areas with particularly stringent indoor air quality requirements. Complete separation of the supply and extract air flows means that no pollutants, moisture, odours or bacteria can be transferred from one to the other. Heating or cooling energy can also be integrated hydraulically in the run-around coil system. The intelligent controller displays the most important operating data and analyses a wide range of efficiency parameters.
The runaround coil system at a glance:
- Complete separation of intake and extract air
- Maximum efficiency thanks to the optimum ratio of heat flows, which can never be achieved by building design alone
- Hydraulic unit with minimised pressure loss, high-efficiency pump with variable output control and precise flow rate measurement using ultrasonic meters
- Optional injection of heating/cooling energy
- Complete integration into the WOLF WRS-K air handling control unit
- Permanent function and performance monitoring
- Includes WOLF commissioning
- Extremely compact design, fits through any door
- Also available in a weatherproof version
- Can now also be controlled using the BMK T10